Yeah, I just ordered a set of 3/8 wobble extensions. That 36 inch guy is right pricey....
I took a look under the car and from the top, and I just can't even see the other bolts on the bell housing that would be above the center line. So I had to break out my flexible shaft camera to see if I could see anything that way. First let me back up a bit.
Just out of curiosity, I went back to the old videos I took while the car was out at Harwood's shop to see what the bell housing looked like, and also to see if Harwood put those bolts in place there.
Yep, looks to me that Harwood did in fact have those bell housing bolts in place. This is right before the drivetrain was put together with the engine and then mated with the car. So it looks to me that those bell housing bolts were in place.
So here's a pic I found online of the bell housing that I have.
I made notations near the bolts that hold the bell housing to the engine block, which can be compared with the bolts in the photos above this one.
Now, back to the flexible camera shots. All of the following pics were taken from the top of the engine, btw. I started on the passenger side, and it appears that both bolts A and B are in place. I didn't try to see if they were torqued down, however, not that I could have gotten a wrench onto them anyway.
BTW, I may have these reversed, as it was pretty tough looking at the photos and figuring out where exactly I was looking at.
Then I went over to the driver side. I believe it is bolt E that is the one I found loose and partially walked out of the threads. I didn't take any further pics of it this time. I tried to find the other two bolts C and D with the flexible camera, and I THINK the only one I was able to find is the one for bolt C.
I'm not positive about this, though, as I found another area that looked like it might be where a bolt goes, but it may just be the tab that is at about the 1 o'clock position in the main picture. I just couldn't get the angle on the flexible camera shaft such that I could see into any threaded hole.
But it appears that at least one other bell housing bolt is completely missing. I'll try again to find where that other bolt is supposed to be, but it won't surprise me in the least to find out that it is missing as well.
So, now the question is, what will it take to simply get to those missing bolt holes to put bolts in them and tighten up the loose one?
I took a look under the car and from the top, and I just can't even see the other bolts on the bell housing that would be above the center line. So I had to break out my flexible shaft camera to see if I could see anything that way. First let me back up a bit.
Just out of curiosity, I went back to the old videos I took while the car was out at Harwood's shop to see what the bell housing looked like, and also to see if Harwood put those bolts in place there.
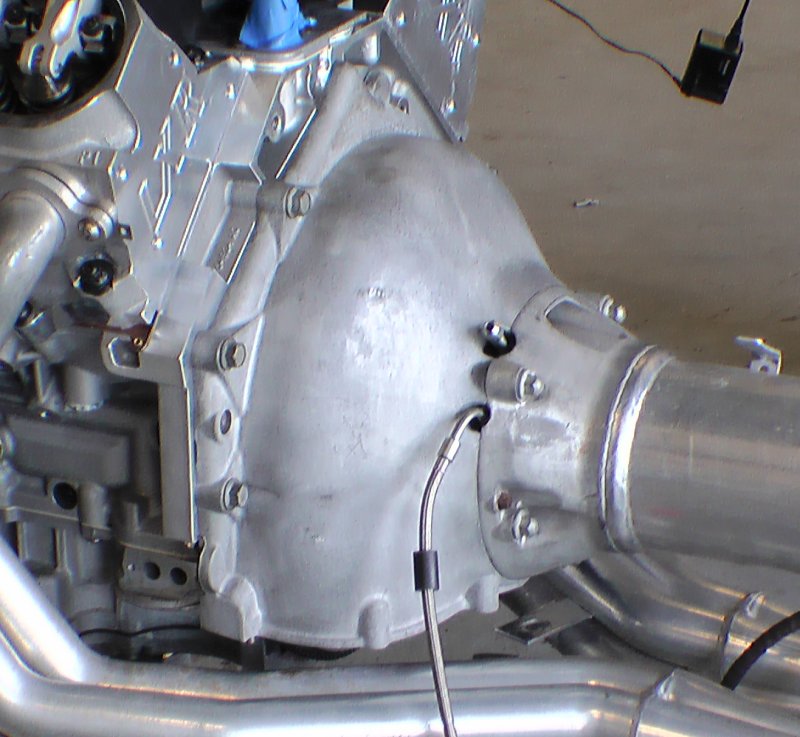
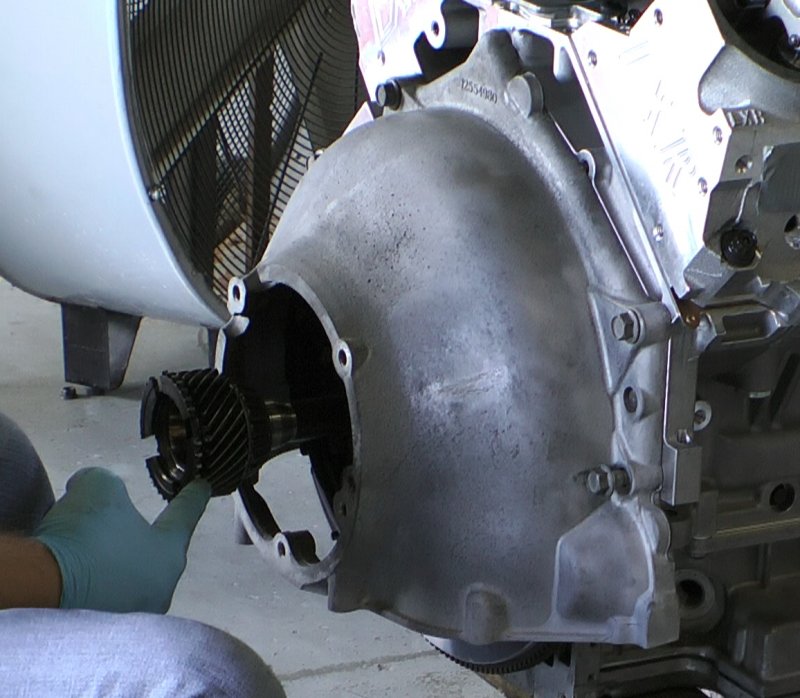
Yep, looks to me that Harwood did in fact have those bell housing bolts in place. This is right before the drivetrain was put together with the engine and then mated with the car. So it looks to me that those bell housing bolts were in place.
So here's a pic I found online of the bell housing that I have.
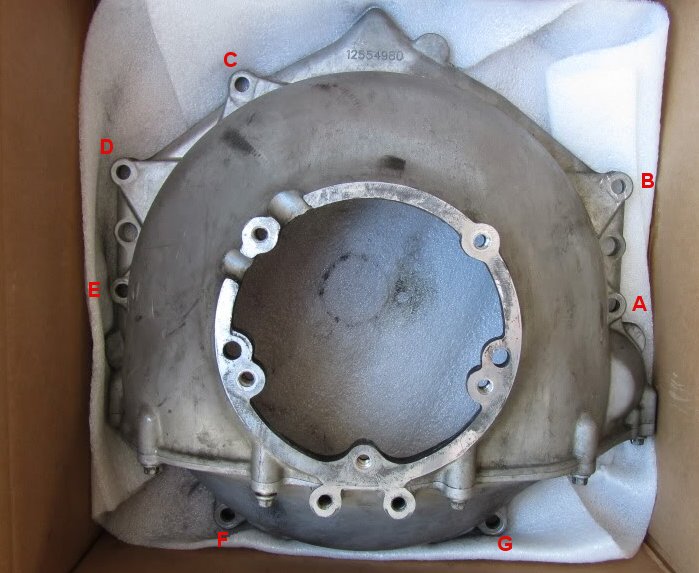
I made notations near the bolts that hold the bell housing to the engine block, which can be compared with the bolts in the photos above this one.
Now, back to the flexible camera shots. All of the following pics were taken from the top of the engine, btw. I started on the passenger side, and it appears that both bolts A and B are in place. I didn't try to see if they were torqued down, however, not that I could have gotten a wrench onto them anyway.
BTW, I may have these reversed, as it was pretty tough looking at the photos and figuring out where exactly I was looking at.
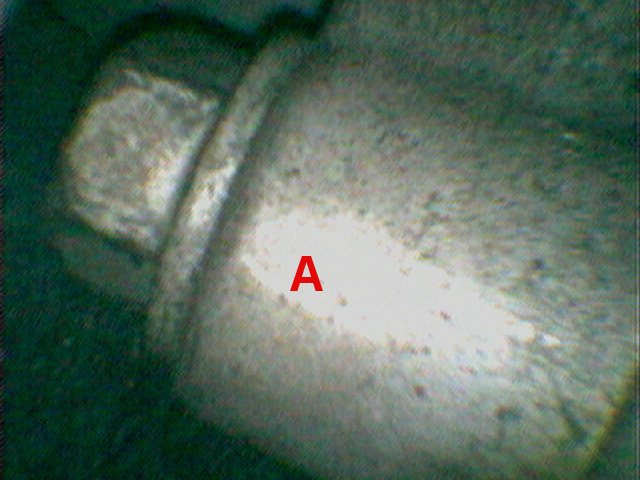
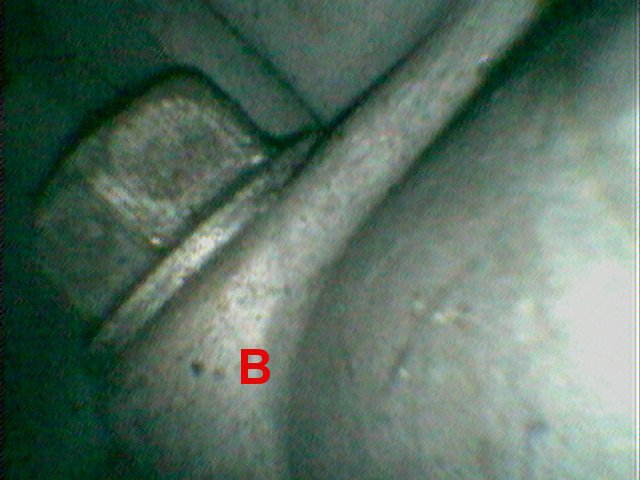
Then I went over to the driver side. I believe it is bolt E that is the one I found loose and partially walked out of the threads. I didn't take any further pics of it this time. I tried to find the other two bolts C and D with the flexible camera, and I THINK the only one I was able to find is the one for bolt C.
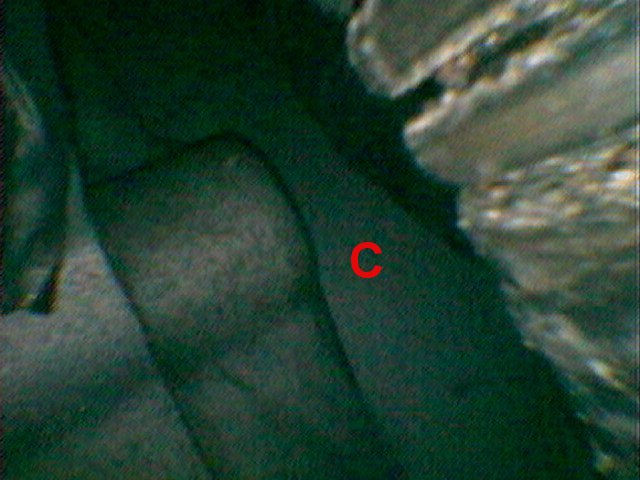
I'm not positive about this, though, as I found another area that looked like it might be where a bolt goes, but it may just be the tab that is at about the 1 o'clock position in the main picture. I just couldn't get the angle on the flexible camera shaft such that I could see into any threaded hole.
But it appears that at least one other bell housing bolt is completely missing. I'll try again to find where that other bolt is supposed to be, but it won't surprise me in the least to find out that it is missing as well.
So, now the question is, what will it take to simply get to those missing bolt holes to put bolts in them and tighten up the loose one?